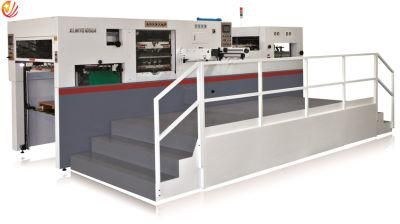
Automatic Die Cutting and Creasing Machine with Stripping Station (XLMYQ-1050A)
Tangshan Jiasun Import and Export Co., Ltd.- After-sales Service:Engineers Available to Service Machinery Overseas
- Warranty:1 Year
- Species:Die Cutting and Creasing Machine
- Imprinting Type:Platen
- Placing Form of Template:Horizontal
- Die Cutting Tool:Metal Mold
Base Info
- Model NO.:XLMYQ-1050A
- Computerized:Computerized
- Automatic Grade:Automatic
- Application:Carton Box
- Model:XLMYQ-1050A
- Max. Paper Size:1040*740mm
- Min. Paper Size:400*350mm
- Die Cutting Precision:Within 0.09mm
- Max. Cutting Speed:7000 S,Hour
- Max. Stripping Speed:6200 S,Hour
- Max. Cutting Pressure:300t
- Sheet Thickness:90-2000g
- Gripper Range:7-14mm
- Feed Paper Pile Height:1610mm
- Delivery Paper Pile Height:1430mm
- Dimension:5833*4167*2758mm
- Total Weight:17t
- Power:3AC,400V,50Hz,N,PE,56kw
- Air Pressure:0.8MP
- Transport Package:Pallet with Film
- Specification:Dimension: 5833*4167*2758mm
- Trademark:Jiasun
- Origin:China
- HS Code:84411000
- Production Capacity:5 Sets,Month
Description
Sheet Thickness
(90-2000g)Corrugated≤4mm 0.1mm≤Paperboard≤1.5mm Gripper Range 7-14mm Max. Cutting Pressure 300T Max. Feeding Pile Height 1610mm Max. Delivery Pile Height 1430mm Total Weight 17T Power 3AC/380V/50H z/PE/ 56 kW Overall Dimensions(mm) 5833*4167*2758mm Air Pressure 0.8MP 2. Features by parts
1) Feeding unit
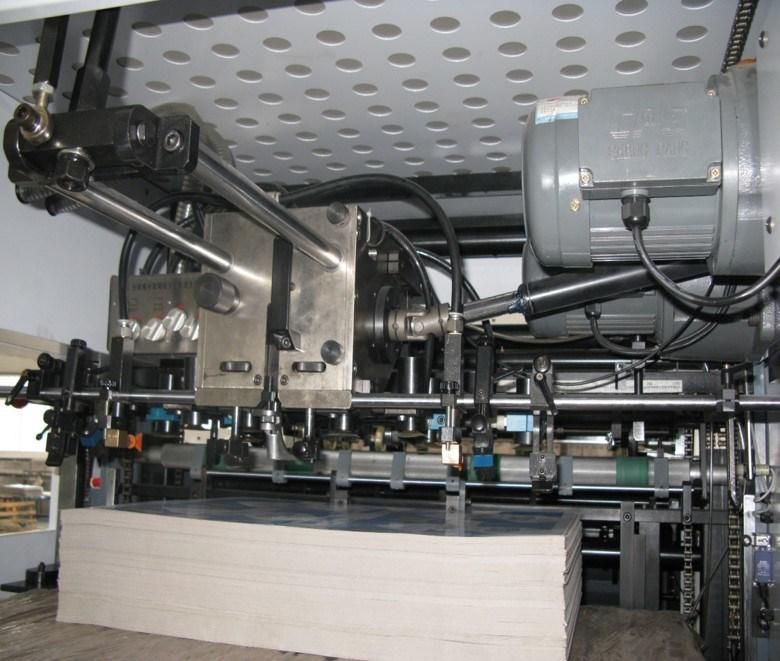
The machine adopts heavy type high speed feeder. Its structure absorbing the most advanced of offset printing machine's feeder design, increase the suction nozzle and delivery nozzle travel and more suitable for different thickness sheet.
By adjusting the inclination angle of the feeder to make the feeding more accurately, to ensure high-speed, smooth delivery.
2) Reduce motor
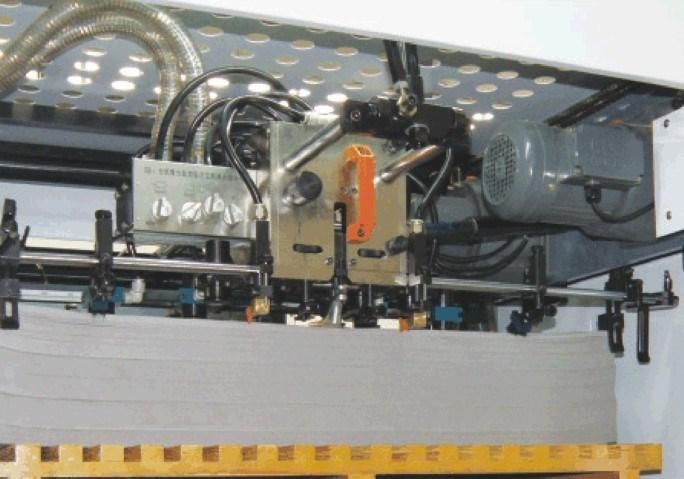
Feeding platform lifting motor adopts Taiwan brand reduce motor, with features of large torque, low noise and safety reliability.
3) Conveyor
Adopts overlapping transmit method, high speed can reach 120 pieces per minute.
Independent design of side blowing device make sheet separation more smoothly; imported Switzerland brand conveyor belts match with rubber wheels and brush wheels, through adjust tension knob to control the sheet tension, ensuring the sheet reach the front lay precisely.
4) Double sheet detection
New design of double sheet detecting device, simple structure, easy operation, sensive and reliable.
5) Side lay
The machine is equipped with advanced push-pul lside lay, can meet the thin paper, thick paper and corrugated sheet positioning needs, and push or pull only need to adjust the pitch on a knurled screw can be completed.
Side photoelectric detection device to monitor the sheet in place. Once the paper is not in place, immediately stop the paper delivery to avoid the production of waste.
6) Front lay and side lay
Non stop adjustment of front lay and side lay.
7) Sheet arrive to front lay adjustment
If the paper arrive to the front lay too early or too late, only need to rotate the hand wheel as the directe sign, which can ensure the sheet moving fast, accurate and smooth.
8) Sheet speed reduction when arrive the front lay
When cutting thin sheet, select the speed reduction mode. When sheet arrive the front lay, it can reduce speed automatically to avoid the high speed sheet crash the front lay.
9) Main parts material
The main worm gear, connecting rod using copper brace connection, manual scraping, strict and precise control of the thermal expansion with the gap, thereby reducing the movement backlash to avoid the impact of worm, worm gear, improve the life of the main drive.
The main parts using high-grade, high-quality ductile iron. The machine wallboard, crankshaft, worm, die-cutting steel and cam are used sophisticated processing equipment and advanced heat treatment process made. Thus ensuring the machine's 8000/hour work speed and 300 tons of work pressure.
10) Pneumatic clutch
Italy OMPI brand of brake clutch, sensitive and reliable.
11) Intermittent gear box
Taiwan brand intermittent gear box, German brand timing belt.
12) Die cutting lubrication
Raining method lubrication system
13) Gripper bar
The machine uses a super-hard aluminum alloy hollow gripper bar, in the 8000 pcs/hour high-speed movement, no vibration, positioning accurately to ensure the stability of die-cutting. Compared with the traditional solid gripper bar, the rigidity is good. It is not easy to be deformed in the high speed movement. The positioning is accurate, the weight is light and the inertia is easy to stop at the time of rapid cutting.
The machine is equipped with high-precision sleeve roller chain manufactured by Renault, UK. It has the characteristics of anti-stretch and light weight. In addition, the chain is equipped with automatic quantitative lubrication system to reduce the elongation of the chain and reduce the noise.
14) Cutting case and plate
High quality alloy material plate and case, easy for opertaion.
15) Cutting plate locking
Pneumatic plate locking
16) Stripping
Top medium and bottom stripping frame. The top and bottom stripping frame can stop when doing non stripping sheets.
17) Sampling
Sheet deliverying aligning can adjust when machine running. Pneumatic control sampling.
18) Sheet delivery adjustment
Non stop sheet delivering function can increase the efficiency.
19) Electrical cabinet
The electrical part of the machine in accordance with the EU CE standard design, a variety of protection are used. Preset counting function is simple and reliable; use the inverter control the main motor to achieve stepless speed, the machine running smoothly.
20) Automatic cutting pressure adjustment
Imported servo motor drive to achieve automoatic cutting pressure adjustment. Multi-electrical switch control to ensure safe and reliable operation.
21) Lubrication system
This machine adopts the Taiwan Weiliang centralized lubrication system to ensure that all the moving parts and some non-refueling parts of the moving parts can be fully lubricated, thus improving the service life of the machine.
22) Oil cooling system
The machine is equipped with a lubricating oil cooling system to effectively reduce the oil temperature, effectively reduce the thermal deformation of sports parts, to ensure stable machine pressure, smooth operation.
(90-2000g)
1) Feeding unit
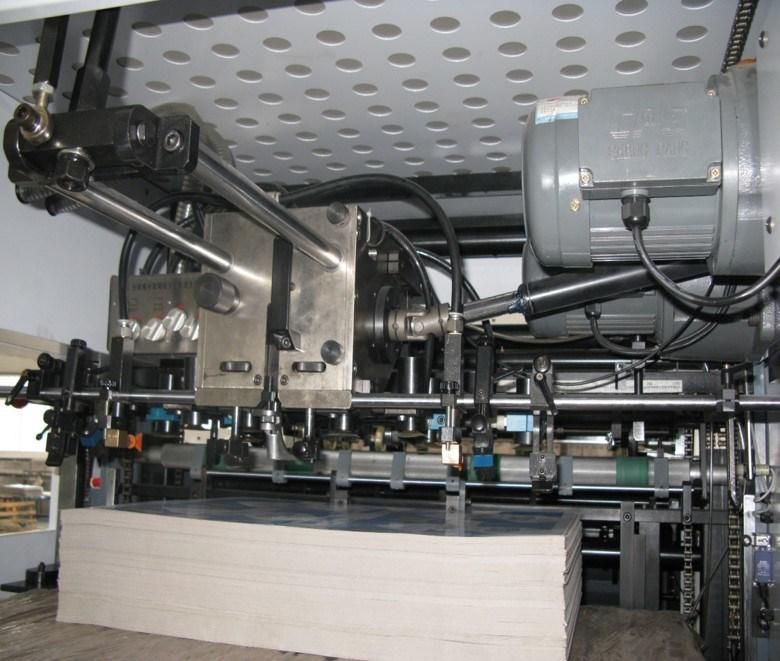
The machine adopts heavy type high speed feeder. Its structure absorbing the most advanced of offset printing machine's feeder design, increase the suction nozzle and delivery nozzle travel and more suitable for different thickness sheet.
By adjusting the inclination angle of the feeder to make the feeding more accurately, to ensure high-speed, smooth delivery.
2) Reduce motor
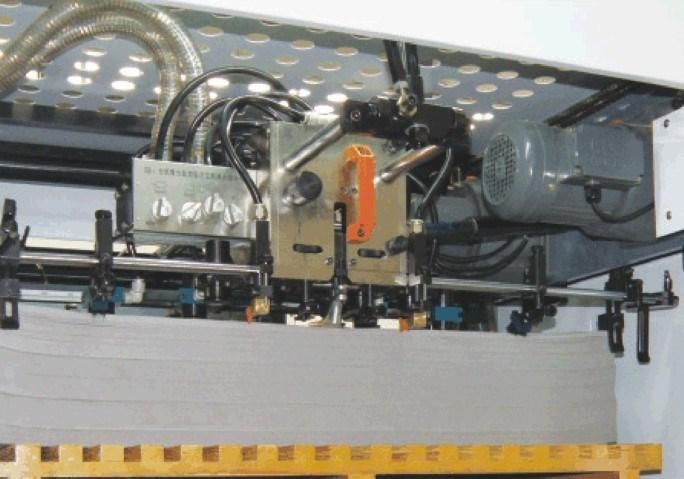
Feeding platform lifting motor adopts Taiwan brand reduce motor, with features of large torque, low noise and safety reliability.
3) Conveyor
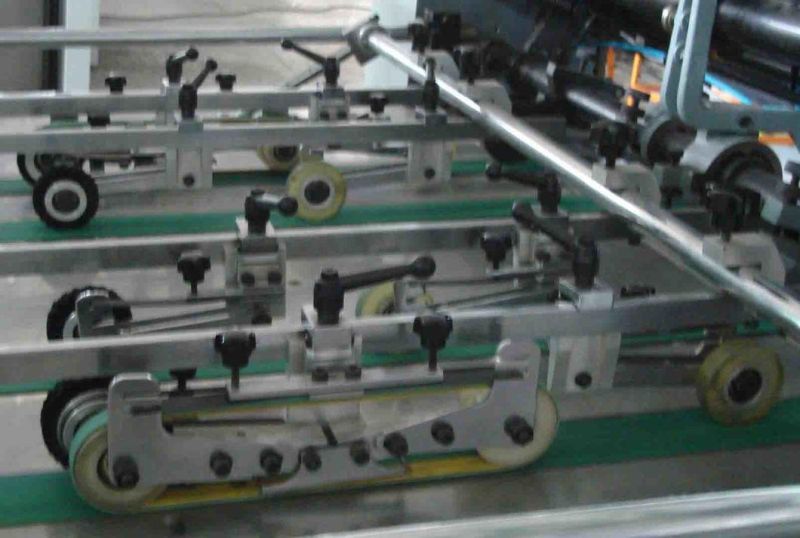
Independent design of side blowing device make sheet separation more smoothly; imported Switzerland brand conveyor belts match with rubber wheels and brush wheels, through adjust tension knob to control the sheet tension, ensuring the sheet reach the front lay precisely.
4) Double sheet detection
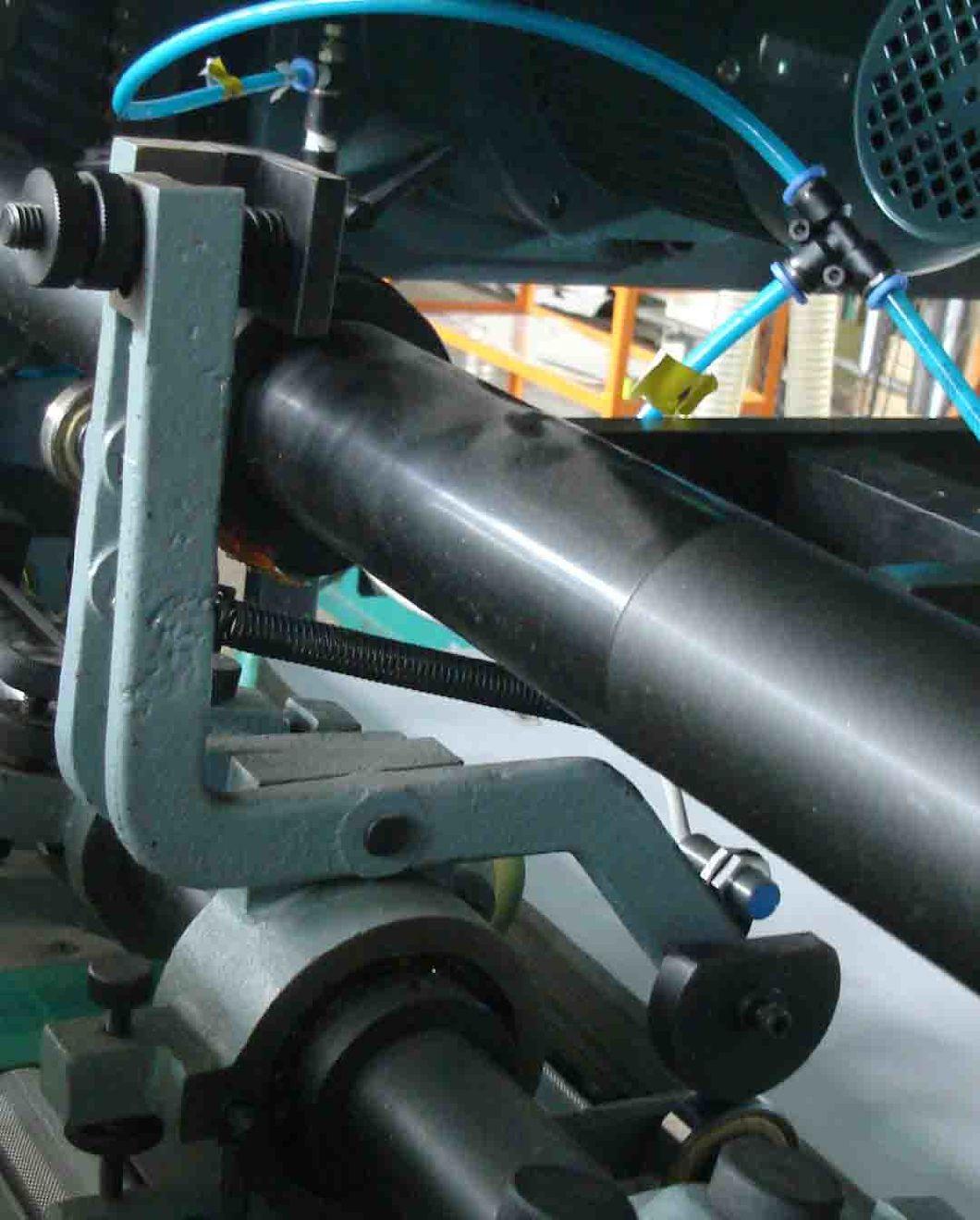
5) Side lay
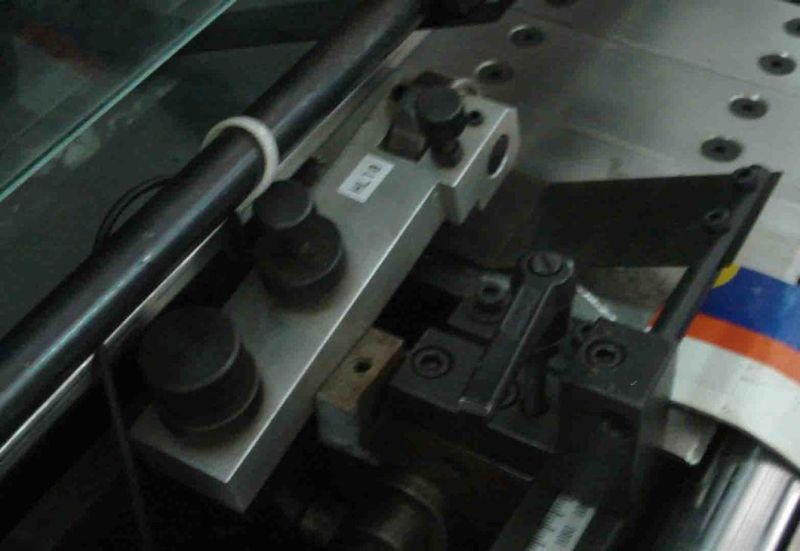
Side photoelectric detection device to monitor the sheet in place. Once the paper is not in place, immediately stop the paper delivery to avoid the production of waste.
6) Front lay and side lay
Non stop adjustment of front lay and side lay.
7) Sheet arrive to front lay adjustment
If the paper arrive to the front lay too early or too late, only need to rotate the hand wheel as the directe sign, which can ensure the sheet moving fast, accurate and smooth.
8) Sheet speed reduction when arrive the front lay
When cutting thin sheet, select the speed reduction mode. When sheet arrive the front lay, it can reduce speed automatically to avoid the high speed sheet crash the front lay.
9) Main parts material
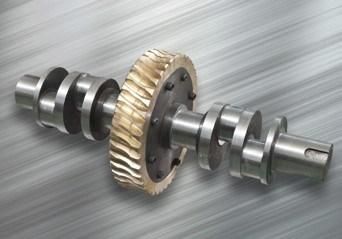
The main parts using high-grade, high-quality ductile iron. The machine wallboard, crankshaft, worm, die-cutting steel and cam are used sophisticated processing equipment and advanced heat treatment process made. Thus ensuring the machine's 8000/hour work speed and 300 tons of work pressure.
10) Pneumatic clutch
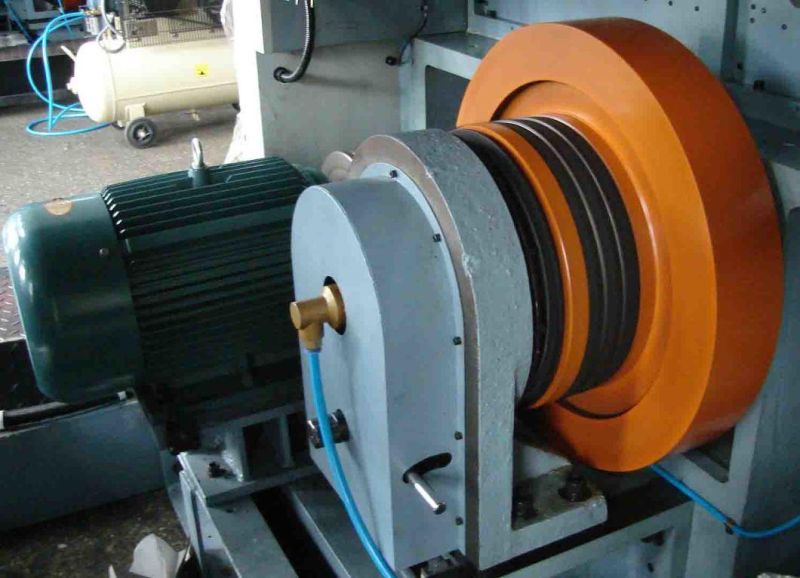
11) Intermittent gear box
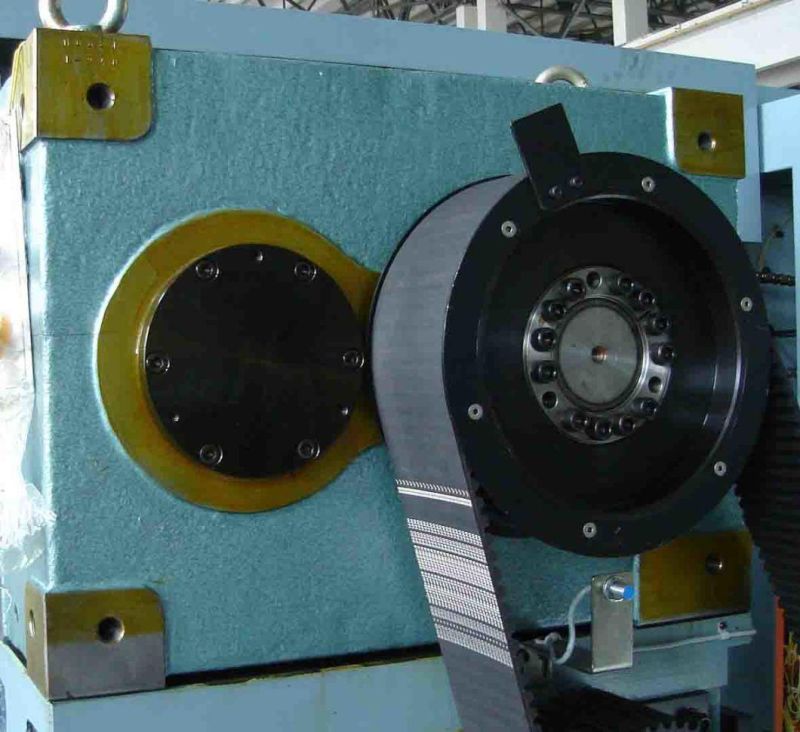
12) Die cutting lubrication
Raining method lubrication system
13) Gripper bar
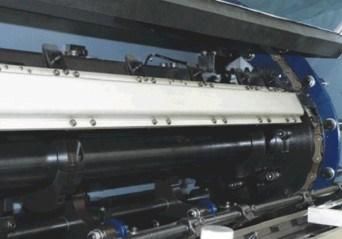
The machine is equipped with high-precision sleeve roller chain manufactured by Renault, UK. It has the characteristics of anti-stretch and light weight. In addition, the chain is equipped with automatic quantitative lubrication system to reduce the elongation of the chain and reduce the noise.
14) Cutting case and plate
High quality alloy material plate and case, easy for opertaion.
15) Cutting plate locking
Pneumatic plate locking
16) Stripping
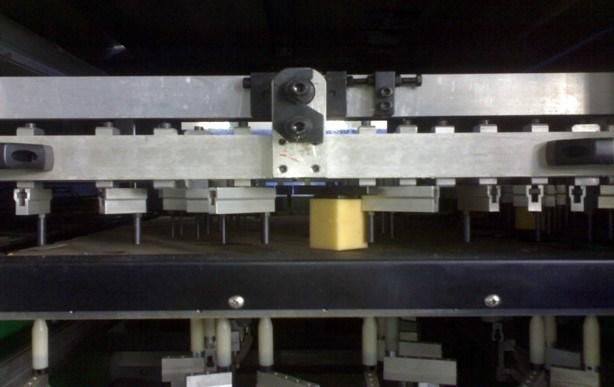
17) Sampling
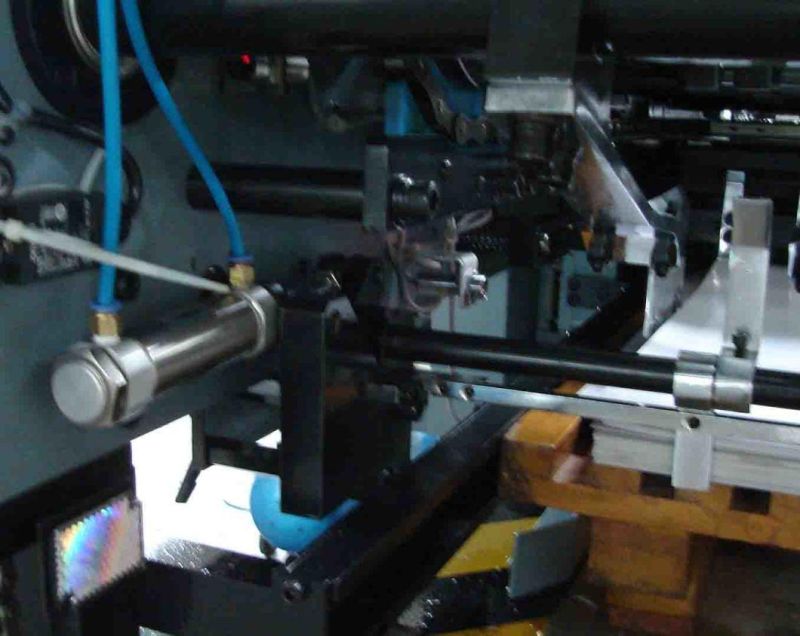
18) Sheet delivery adjustment
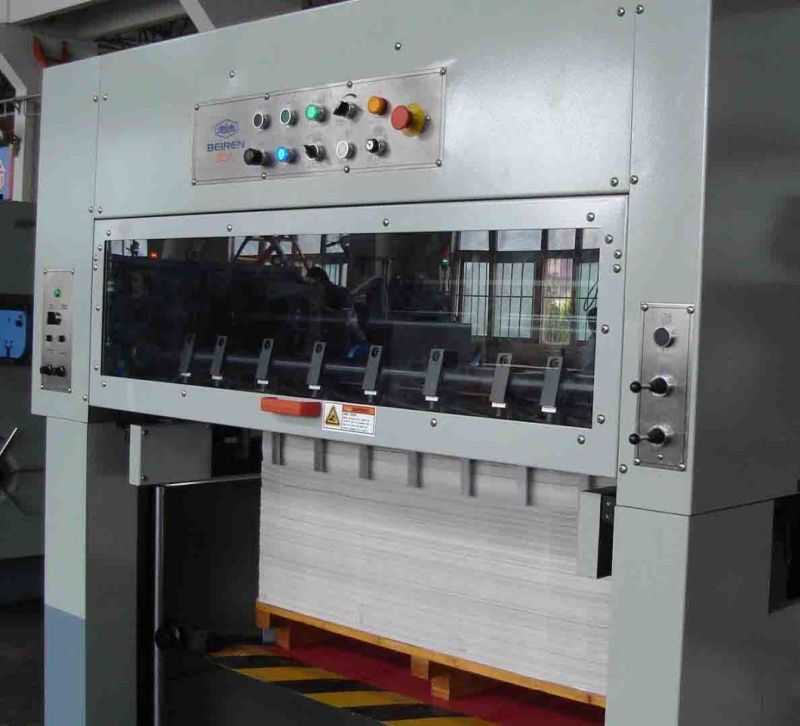
19) Electrical cabinet
The electrical part of the machine in accordance with the EU CE standard design, a variety of protection are used. Preset counting function is simple and reliable; use the inverter control the main motor to achieve stepless speed, the machine running smoothly.
20) Automatic cutting pressure adjustment
Imported servo motor drive to achieve automoatic cutting pressure adjustment. Multi-electrical switch control to ensure safe and reliable operation.
21) Lubrication system
This machine adopts the Taiwan Weiliang centralized lubrication system to ensure that all the moving parts and some non-refueling parts of the moving parts can be fully lubricated, thus improving the service life of the machine.
22) Oil cooling system
The machine is equipped with a lubricating oil cooling system to effectively reduce the oil temperature, effectively reduce the thermal deformation of sports parts, to ensure stable machine pressure, smooth operation.